「すみだモダン」がつないだ職人の魂
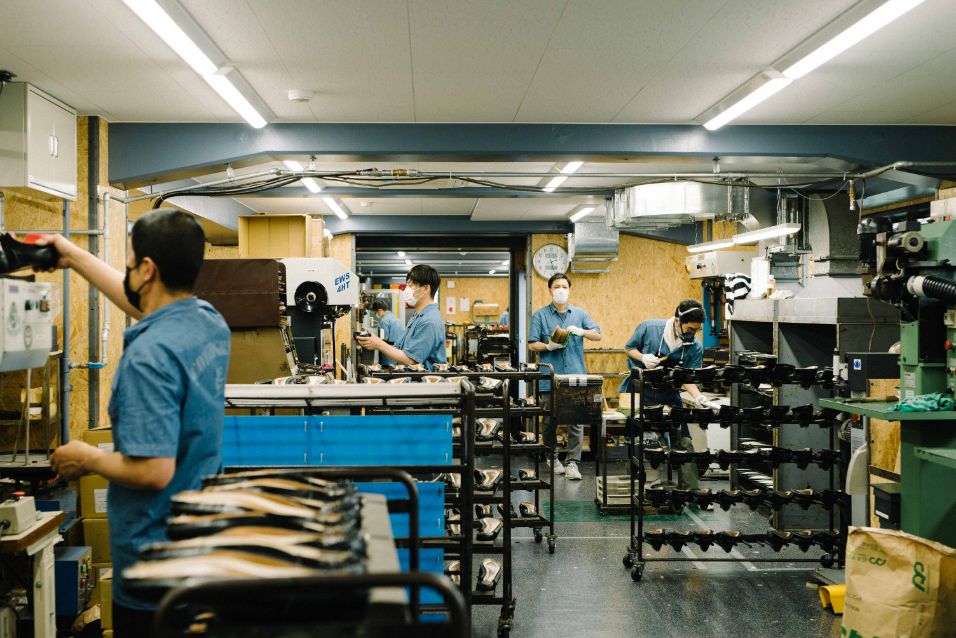
「その頃、スカイツリーが建設中で。通勤途中に見上げるたび『蜘蛛の巣』みたいだな、と思っていたんです」。ヒロカワ製靴の廣川雅一さんは当時試作段階にあった靴を、いつしか「スパイダー」と呼ぶようになった。その靴は、いくつものパーツをパッチワークのように縫い合わせたデザイン。それが、毎朝見るスカイツリーの光景とつながった。完成した靴は、愛称そのまま〈SPIDER- スパイダー〉と名付けられる。
雅一さんが代表を務めるヒロカワ製靴は1964 年に台東区で創業し、1979年に墨田区へ移転した。それ以来、製靴のほぼすべての工程を墨田区の自社工場で行っている。1978 年にはオリジナルブランド〈SCOTCH GRAIN- スコッチグレイン〉を設立。全国の百貨店に販路を広げ、各地に熱心なファンを持つ。〈SPIDER〉も同ブランドの商品だ。
「〈SPIDER〉は片足19枚、合計38枚のパーツを使用するので、裁断した後はパズルのように設計図をつくりながら組み合わせていく必要があります。通常の10 倍くらいの手間がかかってしまうので月に約20 足、多くて40 足までしかつくることができません」
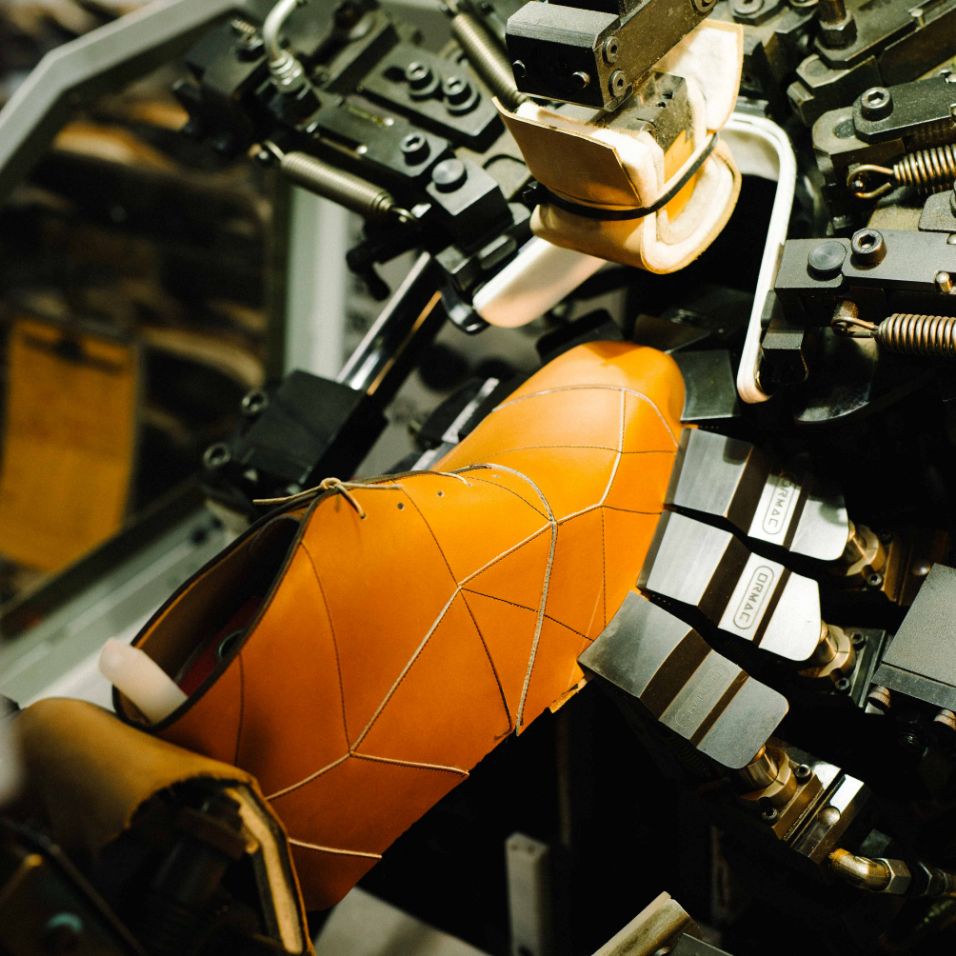
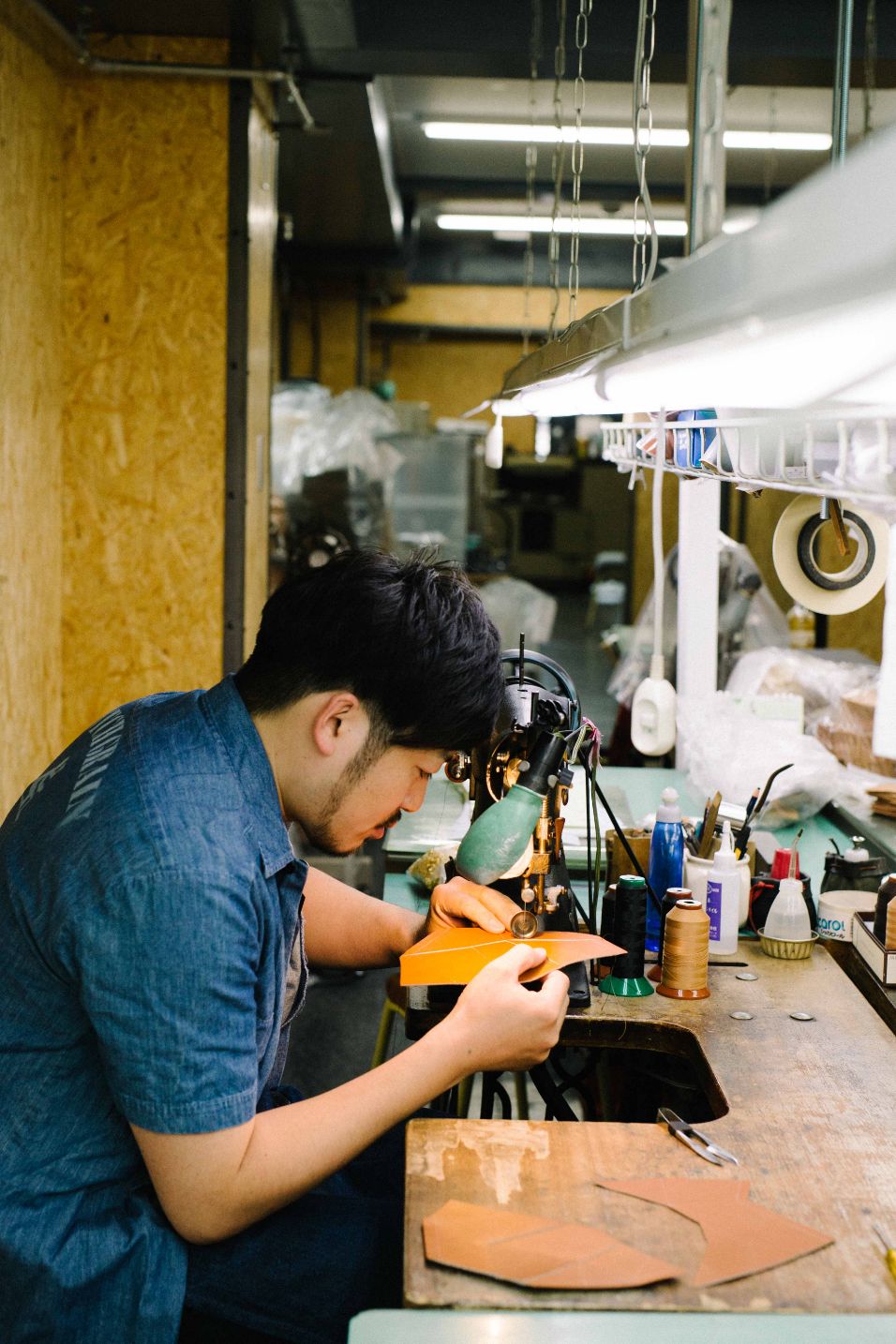
細かいパーツを縫い合わせたデザインには理由がある。「実はこれ、通常の靴には使えないネックレザーという部分を使っています」と言う。
「牛1頭分の一枚革には、首筋あたりにどうしてもシワが目立ってしまう箇所があります。端材となるネックレザーは財布などの小物や、隠れる部分に使ってきましたが、それでも使い切れず、倉庫で山のように眠っていました。それを活用できないかと試作してみたのが〈SPIDER〉です」
シワのあるネックレザーも、うまく切り抜いて縫い合わせれば新たに生まれ変わる。普段は使いづらい部分でも、フランスのビッグメゾンの傘下にあるアノネイ社から仕入れた上質な革だ。ネックレザーもまぎれもなくその一部分。
「磨くと、いい部分と同じように美しいツヤが出るんですよ。手間がかかっても無駄にするよりずっといい。そもそもすごくいい革なんですから、大切に使いたいじゃないですか」
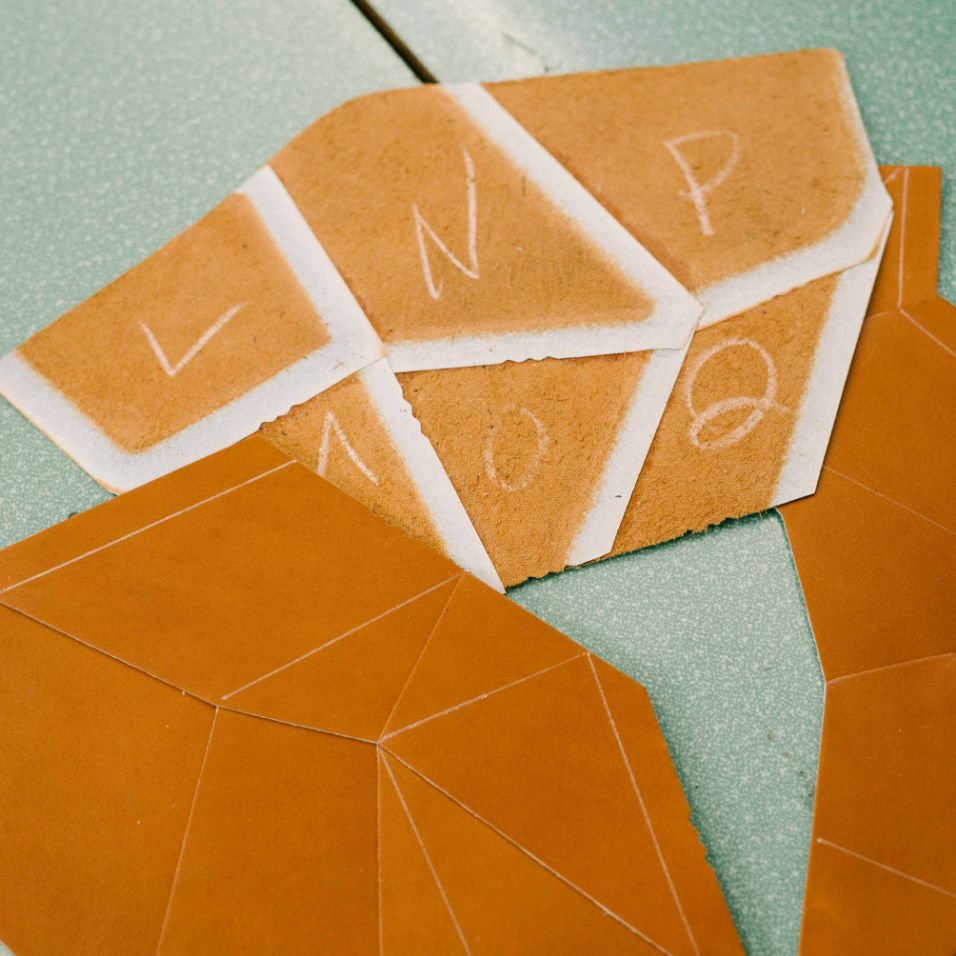
〈SPIDER〉は2009年に墨田区の「ものづくりコラボレーション」事業から生まれた商品。蜘蛛が糸を張りめぐらせたようなデザインはウォーターデザインの坂井直樹さんによるものだ。
〈SPIDER〉は2011 年に「すみだモダン」の認証を受け、2020 年には「ベストオブすみだモダン」に選ばれた。13 商品が選出されたなかでも、最も「すみだモダン」を象徴するプロダクトとして、「ザ・ベスト」に選定されている。
端材の活用を粋な形で提案した点も、サステナブルな産業と社会が求められる現代のあり方と合致しているとして高く評価された。
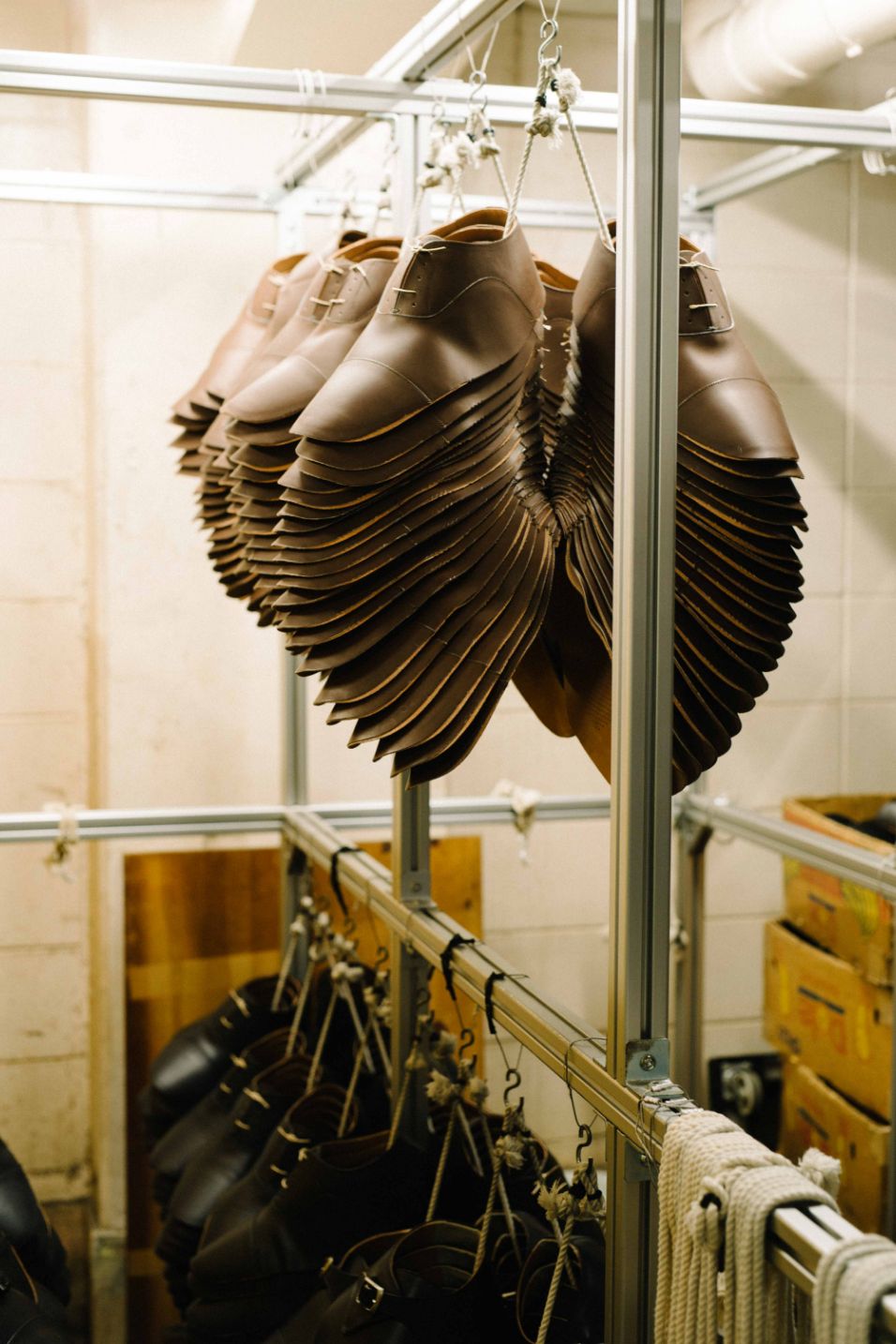
〈SPIDER〉をはじめ〈SCOTCH GRAIN〉の靴はすべて「手入れしていただければ、一生履き続けられる靴です」と雅一さんは断言する。その理由は「グッドイヤーウェルト製法」という伝統技法にある。今から150 年以上前にアメリカのチャールズ・グッドイヤーJr. が世に出した技術で、手縫い靴のよさを「機械縫い」で実現するために考案されたものだ。
ほかの靴製法と比べると工程も使う材料も多く、熟練した技術が必要となる。そのため大量生産には向かない製法で、これを取り入れるメーカーは減る一方だという。しかし手間のかかる分、靴としての安定性と耐久性に優れ、履くごとに足に馴染んでいく。だから〈SCOTCH GRAIN〉はグッドイヤーウェルト製法一本にこだわる。
「グッドイヤーウェルト製法の特徴は、主要なパーツを接着剤で貼り付けるのではなく、縫い合わせながら組み立てていく点です。ミシンで縫う工程は2度あって、最初に縫うのは甲革と呼ばれる靴の上部『アッパー』と、縫いしろの役目を果たす『ウェルト』、足裏が接する『中底』の3つのパーツを1本の糸で『すくい縫い』する。この工程がグッドイヤーウェルト製法の要です」
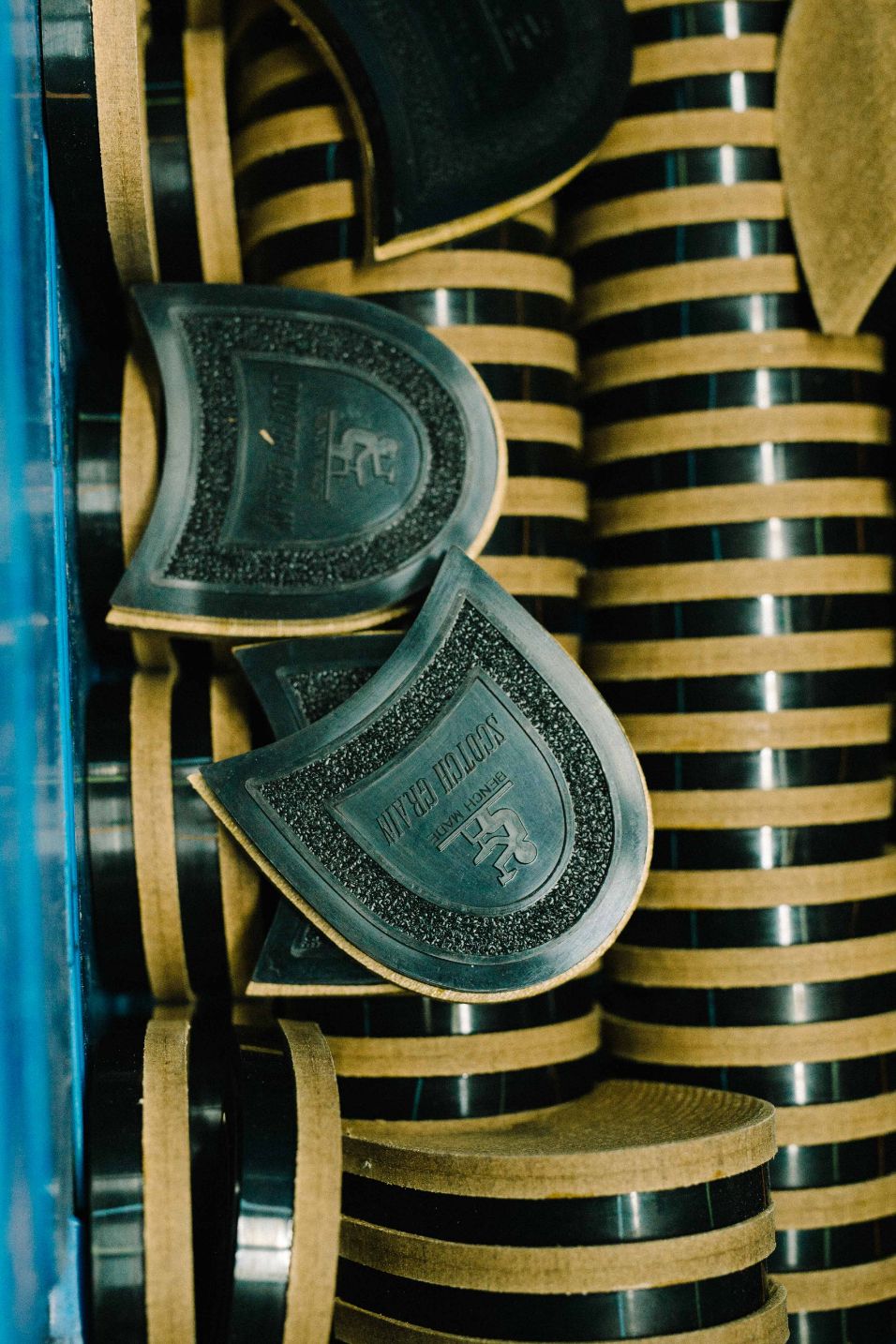
その後、地面に接する「本底」と中底を組み合わせる際にまたミシンが登場する。縫い付けたウェルトと本底を縫い合わせる「だし縫い」の工程だ。
「グッドイヤーウェルト製法の最大のメリットは、縫ってある糸を取れば修理ができ、底の張り替えができるという点」と雅一さん。2 度の縫製工程によって靴底が中底と本底の2 層構造となるため修理を行いやすい。実際に、愛用者の多くは2 度、3 度と底を張り替えるそうだ。コロナ禍に入る前は、ひと月に約1500 足分もの修理の注文が入ってきたという。
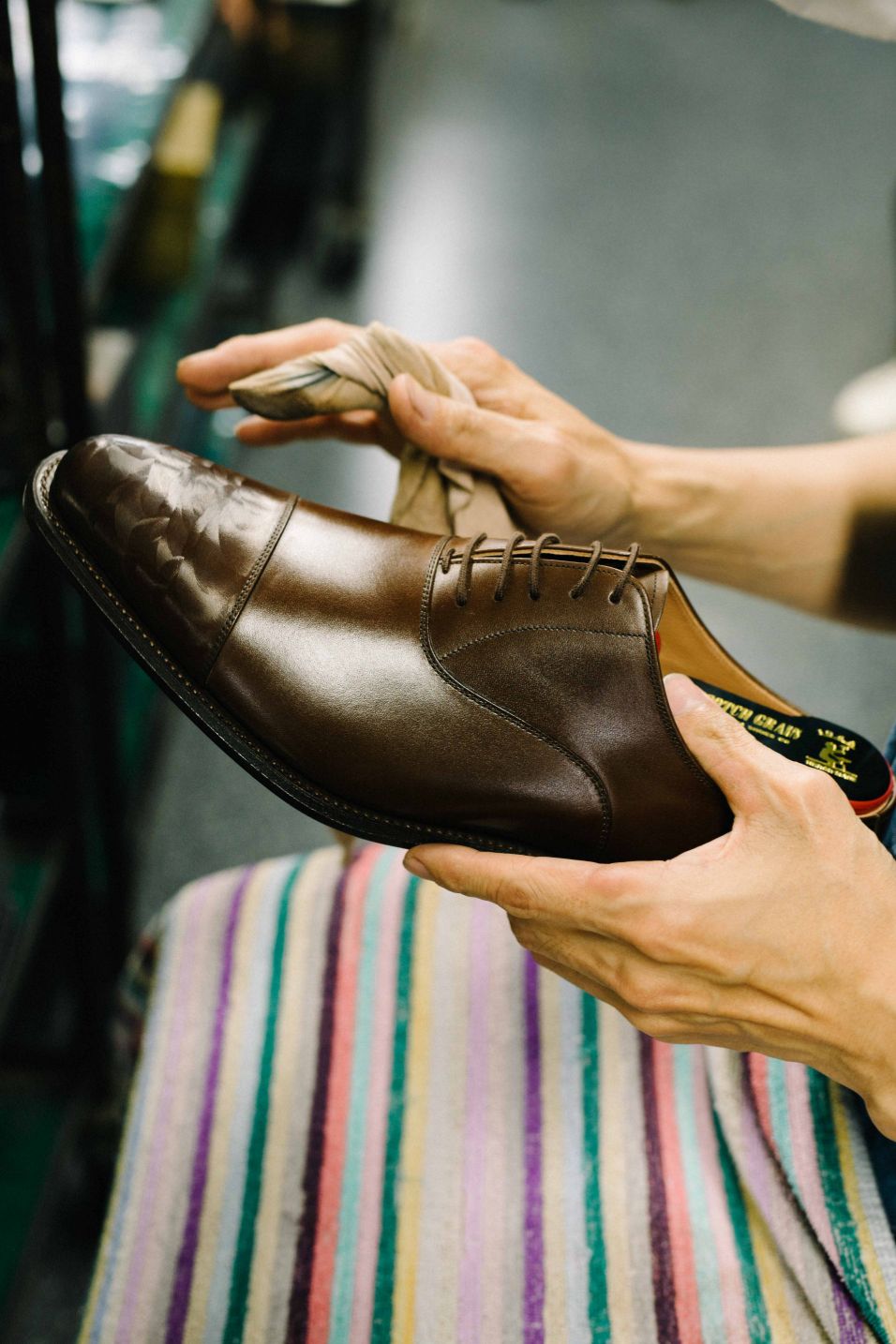
ただ、末長く靴を楽しむためには、使う人自身も日常的に手入れする必要がある。しかし、自宅でのケアを面倒で退屈な時間だと感じる人もいるだろう。このイメージを変えるために〈SCOTCH GRAIN〉はブランドとして顧客に提案していることがある。それが「モルトドレッシング」だ。
「靴磨きでワックスを使うとき、通常は水でのばして磨きます。ただ、お水だと味気ないじゃないですか。だから手前どもはウイスキーを使ってワックスをのばす『モルトドレッシング』をおすすめしています。弊社ではスコットランドのダルモアをパートナーにおすすめしていますが、ご自分のお気に入りのウイスキーでもいいのです。そうやって靴磨きをおしゃれで楽しい時間だと思ってお手入れしてもらえたら」
〈SCOTCH GRAIN〉の工場ではモルトドレッシングでツヤを出す鏡面仕上げ、「モルト仕上げ」も行っている。
「職人が1足あたり約30分かけて、何度も乾かしながら磨き込むことで革の表情に深みが加わります。手磨きでしか行えず、繊細な感覚と経験が必要とされる工程です」
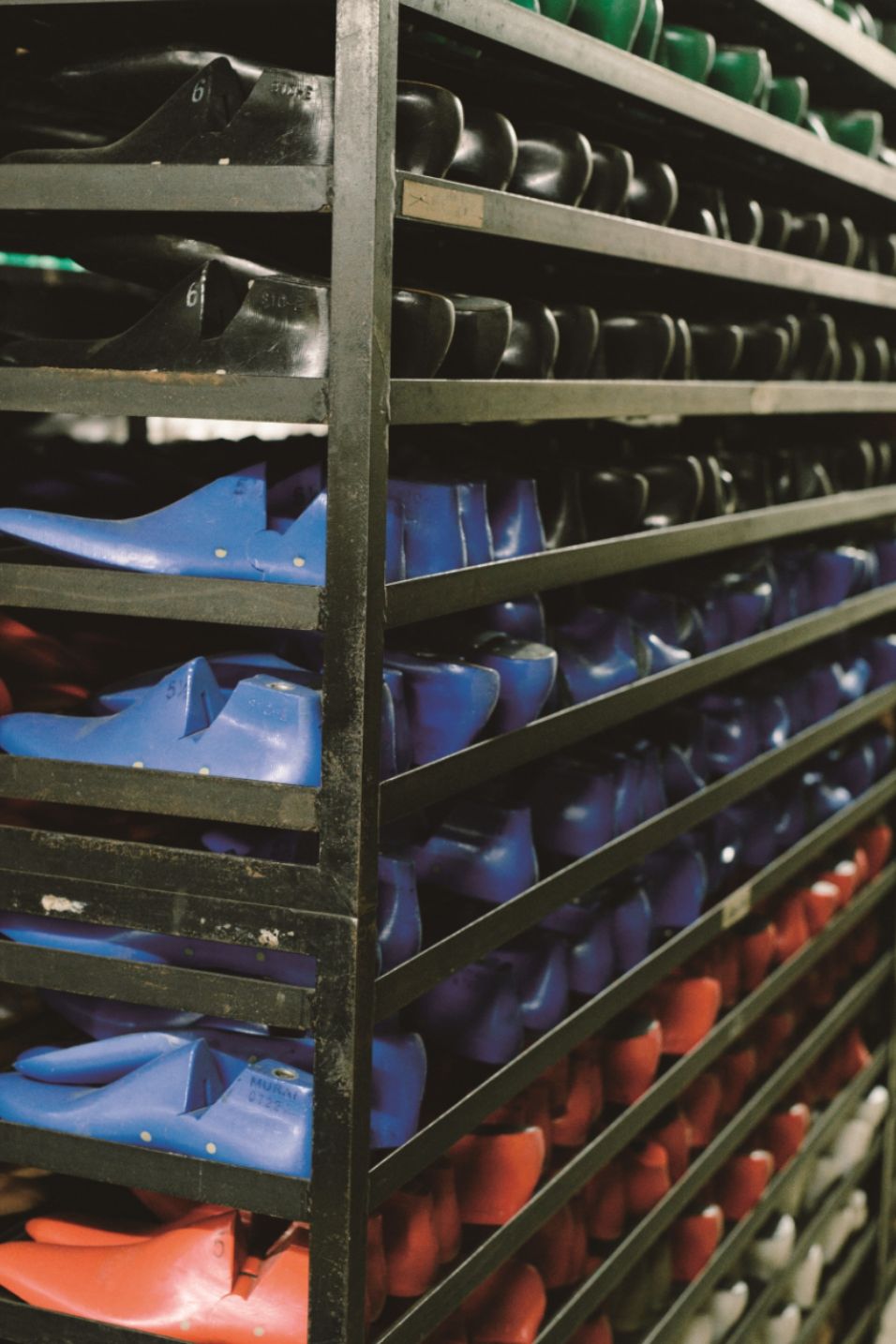
こうした手作業を大切にしながらも、同社の基本はグッドイヤーウェルト製法。つまり機械製靴だ。ここ10 年で主要な機械が新しい年式のものに入れ替わり、2021 年春には工場の改装が完了して、さらなる作業の効率化が可能となった。マシンメイドの靴と聞くと、手仕事の対極にあるものを想像しがちだが、それは違う。
「革は同じように見えて1頭ごとに個性もあり、季節によっても状態が異なります。製靴する際にはその革の状態を見極めつつ、それに合わせて機械を調整しなくてはならない。そこに必要なのが職人の感性と熟練した技術です。どの機械も簡単には扱えません」
もし、すべての工程に機械を用いず手作業のみでつくるとしたら、間違いなく現在のような価格では販売できない。製造できる数も限られてしまうだろう。もとより靴は、展示しておく美術品ではない。生活をともに歩む道具だ。だからこそ、靴が生活者の手に届かない希少な”作品”になってしまっては意味がないと言えないだろうか。
ヒロカワ製靴では、受け継いできた伝統を守りながら、同時に生産性も追求し、工場の機能も、そこで働く職人も進化し続ける。だからこそ上質な靴を適正な価格で多くの人々に届け続けられる。これは真に顧客のほうを向いた選択と言えるだろう。
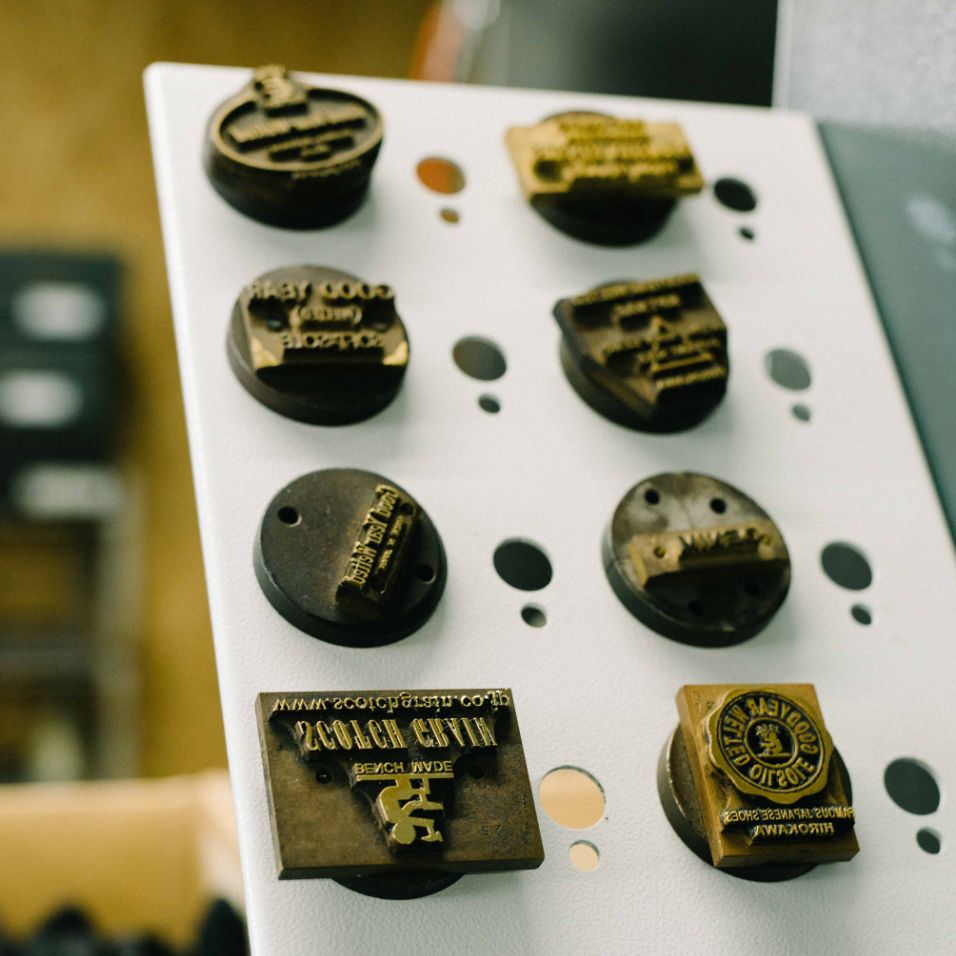
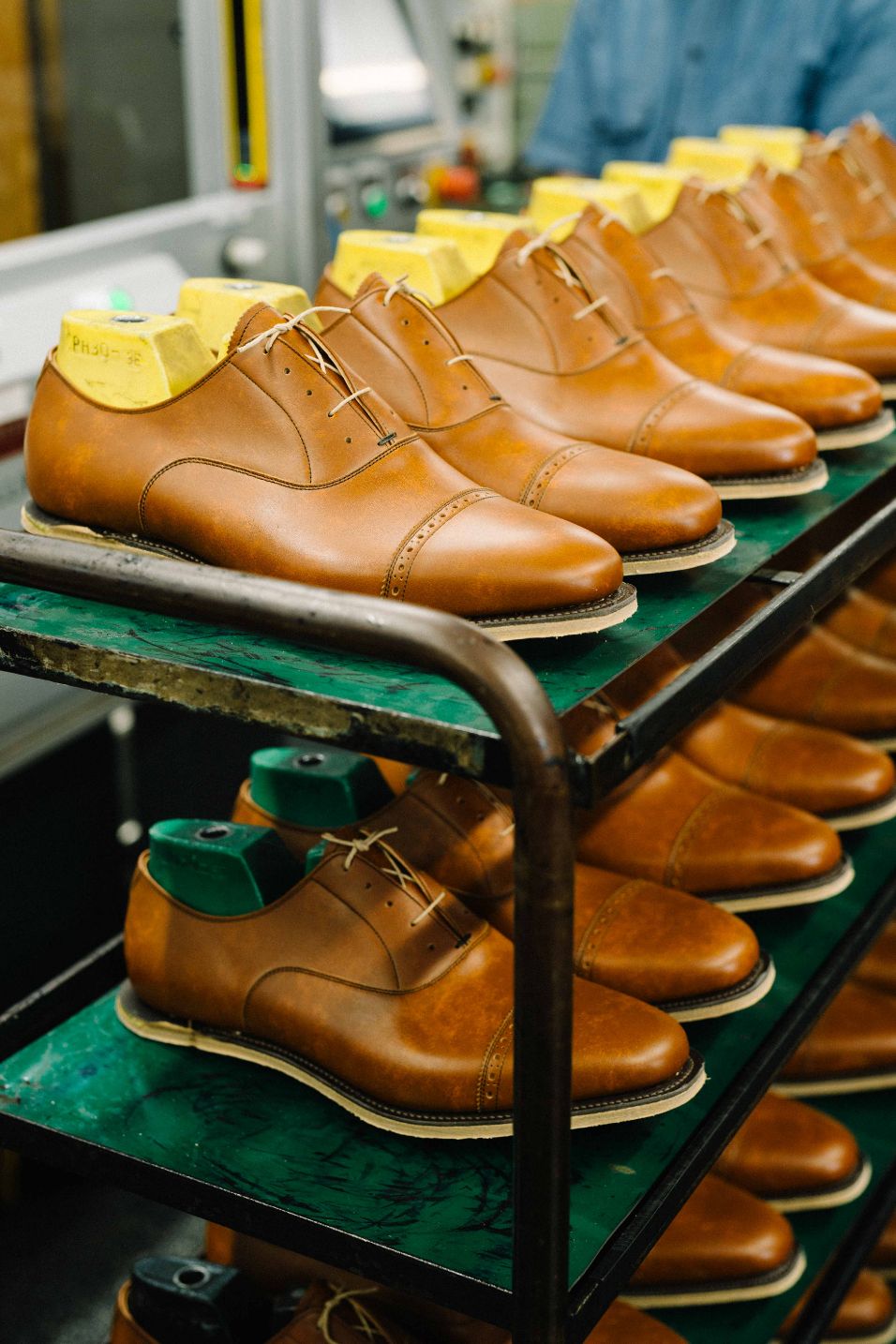
「手前どもの店は、紹介で来られるお客さまが多いんです。『娘の夫となる人に結婚式で履いてほしい』と来店される常連のお父さまや、『いい靴を履きなさい』と後輩の新入社員を店に連れてこられる男性。お酒の勢いで上司が〈SCOTCH GRAIN〉の自慢をされたそうで、居酒屋から同僚のみなさんで店に来てくれ、買ってくださった、というエピソードも聞きました」
直しながら長く履き続けることで、愛しさが募っていく。だから、誰かに教えたくなる、つい自慢したくなる。それが〈SCOTCH GRAIN〉の靴なのだ。
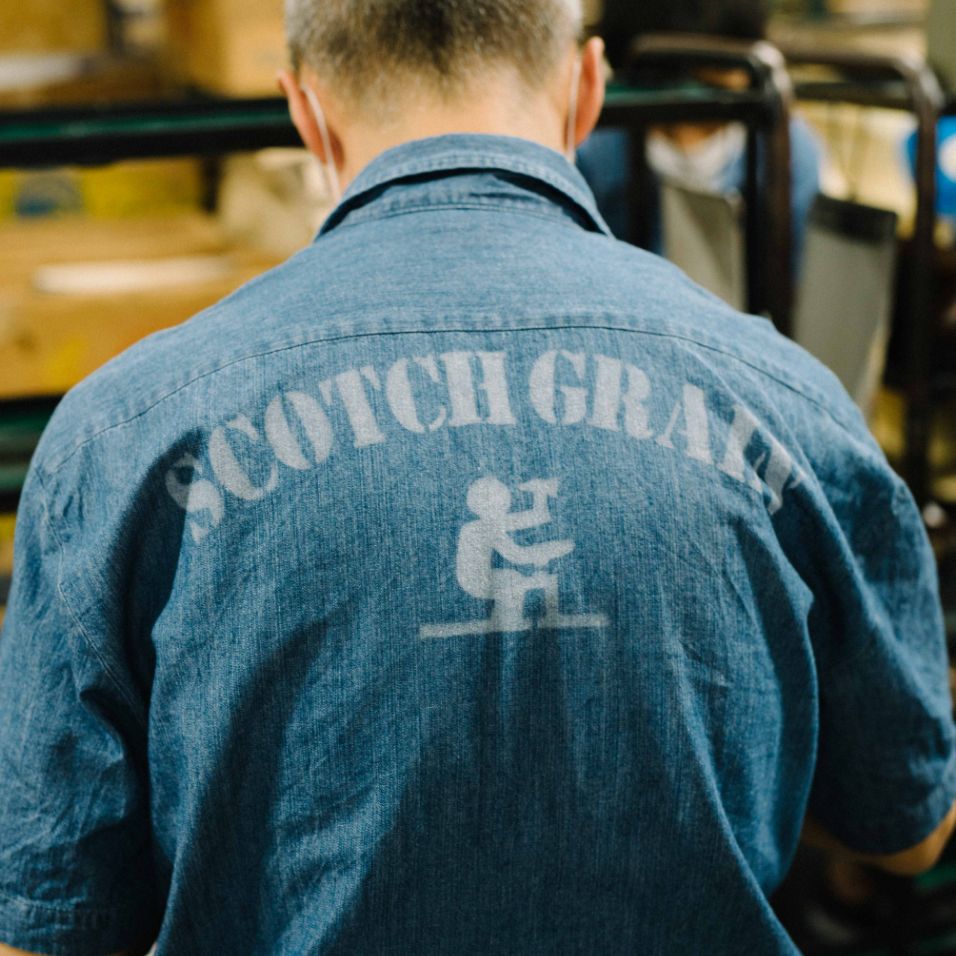
Photo: Kasane Nogawa
Cooperation: Hearst Fujingaho
オレンジトーキョー
代表取締役